
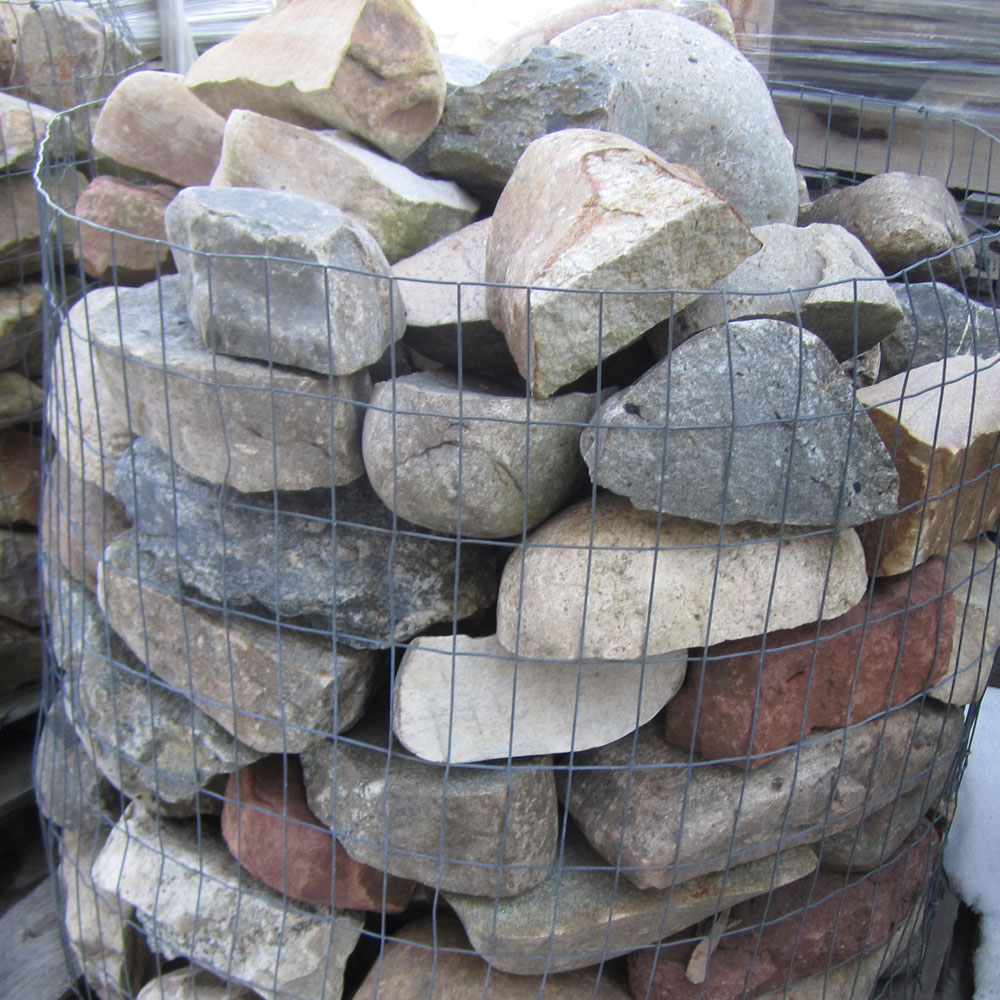
Such stockpiles can grow to enormous size if accumulated over many years. Such stockpiles may not get processed for years, possibly until the mine is depleted or until the mined grades are lower than those in the stockpile. Possibly one or more grade stockpiles may be used, for example a low grade and a medium-low grade stockpile. Grade Optimization: This stockpiling approach is used in situations where the mine delivers more ore than is required by the plant, thereby allowing the best grades to be processed directly while lower grades are stockpiled for a future date. That means even more ore stockpiles at site. Be aware that mining operations might still be mining other ore types, then those ores may need to be stockpiled during the campaigning. At any time the operator can process the material and deplete the stockpile. Such stockpiles will only grow as large as the operator allows them to grow. The problematic ore might be stockpiled until sufficient inventory allows one to process that ore (i.e. Campaigning: For metallurgical reasons if there are some ore types that can cause process difficulties if mixed with other ores.

In my experience there are four main reasons why ore stockpiling might be done. The discussion focuses on the reasons for stockpiling and why stockpiles can get large in size or numerous in quantity. In this blog I won’t go into all the costs and environmental issues associated with stockpile operation. To many stockpiling may seem like a good idea until they saw it in action. In some cases it was apparent that not all team members were clear on the purpose of stockpiling or had preconceived ideas on the rationale behind it. However sometimes team members were surprised at the size of the stockpiles that were generated by the production plan. In many of the past mining studies that I have worked, stockpiling strategies were discussed and usually implemented.
